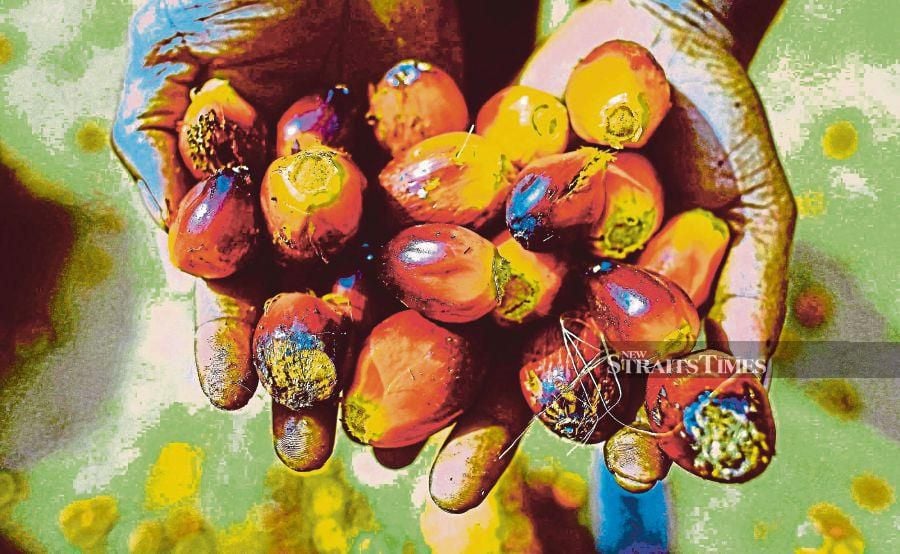
THE issue of labour shortage in oil palm plantations in the country has been getting the attention of the media lately. Measures are already in place to address the issue and strategies are being formulated to ensure the competitiveness and sustainability of the Malaysian palm oil industry.
The oil palm plantation sector which relies heavily on labour, particularly for maintenance activities and harvesting of fresh fruit bunches (FFBs) faced severe labour shortage during the Covid-19 pandemic in the past two years as foreign workers had to leave the country.
This has affected the crude palm oil (CPO) production which declined 3.6 per cent to 19.1 million tonnes in 2020 compared to 19.9 million tonnes in the previous year.
In 2020, the shortage of labour in the plantation sector increased by 6.0 per cent compared to that of the previous year due to the freeze on applications to hire foreign workers by the government.
Meanwhile, the freeze on the entry of Indonesian workers to Malaysia implemented by the Indonesian government in 2021 has caused the total shortage to rise by 24.9 per cent compared to the previous year which contributed to the decline in CPO production to 18.1 million tonnes, a fall of 5.4 per cent.
Last year, about 391,000 workers were employed in the oil palm plantation sector. Out of the total, 74 per cent were foreigners, mostly Indonesians. This indicates that the sector is still not attractive enough to attract the local workforce due to the 3D (Dirty, Difficult and Dangerous) stigma.
Based on Malaysian Palm Oil Board (MPOB)’s data, in August this year, the oil palm plantation sector’s total labour requirement was 437,212. However, the number of workers in the sector was 382,582, recording a shortage of 54,630.
The reopening of borders will ease the problem. But, the use of machineries in oil palm plantations will reduce dependency on foreign workers.
MPOB has developed and innovated 35 breakthrough technologies to ease fieldwork and improve plantation efficiency and labour performances and several of them have already been commercialised.
Among the inventions are Hydra-Porter, a hydraulically- powered 4-Wheel FFB transporter, harvesting tools namely Cantas and Cantas Electro, The Grabber, Beluga, sensor-based spraying vehicles, and FFB Mobile Lifter, which have been introduced to the industry.
MPOB also embarks on high-tech R&D projects which include laser technology, ultrasonic transducers, radio coordinating (RC), robotics, and various harvesting technologies.
The launch of the Mechanisation and Automation Research Consortium of Oil Palm (MARCOP) in November 2021 as a collaborative effort between the government and the industry to enhance technology adoption in the field, will reduce dependency on the labour requirement for oil palm harvesting.
MARCOP ensures that innovations in the mechanisation and automation technologies fulfill the need of the oil palm plantation sector.
MARCOP’s three-pronged strategies target short, medium and long-term outcomes. In the short-term, MARCOP targets to improve the existing oil palm mechanised cutter. The improvement is expected to increase the labour to land ratio up to 1 to 25 hectares.
On the other hand, the medium-term strategies predict that artificial intelligence and sensors technologies could double up the labour to land ratio up to one to 50 hectares.
Meanwhile, the long-term strategies target the robotic technologies adoption to increase up to two folds of the labour to land ratio of the predecessor target.
The use of future machine tools which would have to be more sophisticated, safe and utilising green energy is apt as we move into the new era industry-the fourth industrial revolution or IR 4.0.
Additionally, the machines should also be semi-automated, so that more locals are attracted to work in oil palm plantations. We may see the harvesting tools and cutters using robotic technology in the future.
The future machines must also accommodate narrow terraces and difficult terrains which are common in the country. On the other hand, land for oil palm plantations should also be prepared to accommodate the machines.
The government, through MPOB has also set up the Malaysian Palm Oil Training Centre (PLASMA) which provides knowledge on plantation management and machine operating system to enhance capability and understanding in the oil palm industry.
Until December 2021, PLASMA has trained 2,237 youths at its centre in PLASMA Keratong, Pahang and over 55 per cent of them have entered the plantation sector, especially those involving the handling of machineries.
With the commitment of industry players, these measures and strategies will address the issue of labour shortage in the country’s oil palm plantation sector, minimise operational cost and improve the yield of palm oil which in turn will increase the income of players including the smallholders.
* The writer is the director-general of Malaysian Palm Oil Board
Source : NST